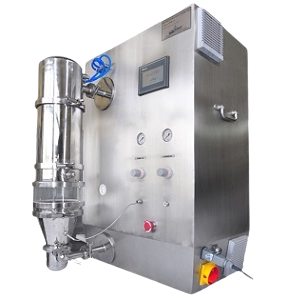
Unveiling the Fluidized Bed Processor (FBP) in Pharmaceuticals
The Core Principle
The Fluid Bed Processor for Granulation (FBP) revolves around the concept of a fluidized bed of solid particles, through which hot air is propelled at high pressure via an air distribution plate situated at the container’s base. The magic lies in the hot air that continuously suspends the particles in an airy state for drying, a state commonly referred to as a fluidized state.
The process involves the spraying of granulating liquid or coating solution onto fluidized granules or particles, followed by thorough drying with hot air. These critical spray techniques in FBP are categorized based on the position of the spray nozzle:
Top Spray:
- Ideal for wet granulation, coating, and drying.
- The spray nozzle is located above the expansion chamber.
- Coating liquid is sprayed down onto a bed of fluidized particles.
- Designed for coating substantial quantities of powder, crystals, or pellets.
Bottom Spray (Wurster Fluid Bed):
- Widely popular in the pharmaceutical industry for drug layering and for coating to modify or control drug release.
- Hot air is passed through the fluid bed, lifting particulate material in the air stream, and a solution/suspension is sprayed onto the fluidized bed for granulation and coating.
Tangential Spray:
- The nozzle is introduced at the side of the product container or expansion chamber.
During processing, three mechanical forces come into play, causing particle movement, mixing, and granulation:
- The spinning of the disk generates centrifugal force.
- The lifting force results from the hot air passing through the adjustable disk gap.
- Gravitational force causes material to fall onto the disk.
These forces combine to ensure proper mixing, leading to granule formation, effective drying, and coating with excellent content uniformity.
The Components of FBP
The granulation chamber is comprised of several parts:
- Base part
- Movable product equipment parts, such as top and bottom spray, and tangential spray
- Expansion chamber
- Filter chamber
The Exhaust Air Handling Unit consists of:
- Stainless Steel 304 Impulse Back Blow Dust Collection
- Temperature Sensor
- Differential Pressure Meter
- Exhaust Air Recycling
- The polyester cartridge filtration is anti-static. It can be cleaned by blowing compressed air or washing with water.
- Exhaust Air Recycling (optional feature)
- Air Handling Unit (AHU) of FBP
The Inlet Air Handling Unit comprises:
- Pre-filter G4
- Intermediate Filter F8
- Wheel dehumidification
- Electric heating system
- Cold & Hot Air Valve
- Final Filter H13
- Temperature & Humidity Sensor
How It Works
To dry the bowl, hot filtered air is passed through it. Simultaneously, granule particles are suspended in the air after being lifted from the bottom of the bowl by an airstream. During this phase, granules are coated with a coating solution spray using the top, bottom, and tangential spray options provided with the chamber unit.
Process Parameters in Fluid Bed Coating
- Inlet Temperature:
- The inlet temperature directly affects the drying of particulate materials.
- High temperatures can lead to the development of static charges.
- Increased inlet air temperature results in a decrease in average granule size.
- Atomization:
- Atomization of the coating solution on the fluidized bed depends on atomization air pressure.
- It provides a solution to the challenge of spraying the solution on the fluidized bed.
- Blower Speed:
- High air flow can lead to attrition and the generation of fines.
- Proper bubbling is necessary for uniform coating and drying.
- Partition Column or Air Distribution Plate:
- The partition height is determined by particle size, substrate density, and the desired velocity of particles entering the coating zone.
- Selection of the air distribution plate and partition height affects the fluidization of particles.
- Spray Rate/Pump:
- Spray rate is determined by the drying capacity of the equipment and the area of the air distribution plate.
- Spray rate directly affects droplet size.
- A peristaltic pump is used for maintaining a constant spray rate.
- Relative Humidity:
- Changes in relative humidity can result in sticking or the formation of lumps.
- Decreasing relative humidity can lead to the development of static charges.
- Increasing relative humidity can cause the formation of lumps.
- Strength of Coating Solution:
- The strength of the coating solution plays a significant role in nozzle blockage.
- An increase in the strength of the coating solution can lead to nozzle blockage due to higher viscosity. However, it should not be too concentrated or overly diluted.
Applications/Uses
- Enhancement of product quality.
- Creation of sustained-release coatings and enteric coatings for drugs.
- Cost reduction in manufacturing, manpower, and time.
- Protection of active components from atmospheric degradation.
- Taste masking of unpleasant drugs and improvement of taste through sugar coating.
A fluid bed processor stands as a versatile and indispensable tool in pharmaceuticals, enabling a wide range of critical processes essential to the industry’s success.