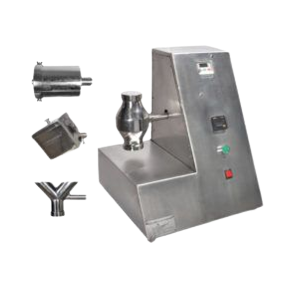
The Double Cone Blender: Mixing Excellence in Pharmaceuticals
The Science Behind It
At the heart of the double cone blender lies a simple yet effective principle – the magic of tumbling motion. This apparatus excels in the precise dry mixing of free-flowing solids, making it an indispensable tool in the pharmaceutical industry. What sets it apart is its ability to alter both the bulk density and the proportion of each solid component in the mixture.
As the double cone rotates, materials continuously engage in a mesmerizing dance of combination, resulting in a perfectly blended mixture. The process typically takes around 10 minutes, though this duration can vary depending on the complexity of the blend.
Constructed for Perfection
The construction of the double cone blender is a marvel in itself. Its main body comprises a central cylindrical segment that seamlessly connects two cylindrical cones. The axis of rotation parallels the cone axis and passes through the cylindrical section.
One of the lateral supports houses the blender motor, while the construction material itself is stainless steel. The blender is meticulously crafted, with Argon arc welding ensuring a mirror-like finish both inside and outside. It features a butterfly valve for easy material discharge and cleaning at one end, along with a hole fitted with a cover that can be opened at the other end. Stainless steel baffles inside the blender further enhance the mixing process.
An additional provision for a liquid spray system allows for the introduction of liquids in spray form during the blending process. Furthermore, a vacuuming device with self-cleaning hoses ensures the automatic loading of powders and granules into the blender body.
The Workings Unveiled
To achieve impeccable mixing results, the powder is filled up to two-thirds of the blender’s volume. The blender’s rotation speed typically ranges from 30 to 100 revolutions per minute, creating a tumbling motion that results in perfect mixing. The finished product can be conveniently discharged from the bottom of the equipment.
What’s more, the mixing tank can be tilted anywhere from 0 to 360 degrees, offering flexibility for discharging and cleaning operations.
Advantages of the Double Cone Blender
- Ease of Maintenance and Cleaning: This equipment is designed with simplicity in mind, making maintenance and cleaning a breeze.
- No Material Clogging: Say goodbye to worries about material getting stuck in corners – the design prevents clogging.
- High Capacity: It can handle substantial quantities with ease, making it perfect for large-scale operations.
- Versatile for Varying Densities: The double cone blender efficiently mixes powders of different densities, offering versatility.
- Minimal Wear and Tear: The equipment experiences minimal wear, ensuring a longer lifespan.
Drawbacks to Consider
- Not Ideal for Fine Powders: It struggles with handling fine powders effectively.
- Limited Shear: Due to low shear capacity, it might not be the best choice for blending fine and large particles together.
- Space Requirements: The double cone blender demands a fair amount of space, so it may not be suitable for areas with low ceiling heights.
Applications Across Industries
The double cone blender finds its applications in various industries, including pharmaceuticals, foods, chemicals, and cosmetics. It’s an ideal solution for:
- Mixing dry powders or granules into tablet and capsule formulations.
- Blending dry granule sublots in bulk lubrication stages to increase batch sizes.
- Transitioning wet powder to dry powder with efficiency.
- Enhancing the mixing quality of granular and powdery materials in a wide range of industries, including chemical, plastic, rubber, food, essence, dye, and dyeing.
In the world of pharmaceuticals and beyond, the double cone blender reigns supreme, offering a perfect blend of science and efficiency.